success stories
Minimizing food waste with Kemutec Cone Mill
Share
Kemutec Cone Mill versatility provides customer with confidence to expand into new product line
Food loss and waste is food that is grown or produced but not consumed. It is considered a significant contributor to the impact of agriculture on climate change as well as influencing environmental issues, such as the use of land, water, and the loss of biodiversity. Food loss and waste amount to a staggering 3.3 billion tons of CO emissions annually. Preventing this across the entire value chain is therefore essential to contribute to a more sustainable future.
Huntapac Produce Ltd is a fourth-generation family-owned business based in a small village in Lancashire, England. They specialize in the growing, packing, and distribution of root vegetables. In 2020, they began exploring a new, more sustainable processing service that used bruised products that would be wasted otherwise. To help facilitate this, they were looking for an experienced cone mill supplier.
Kemutec, part of Coperion, specializes in food powder processing technology, equipment, and systems and was expertly placed to support Huntapac Produce in meeting its unique needs. Kemutec was recommended to Huntapac by R Simon Dryers, a long-term client of Coperion, who knew that our expertise and technology was the best in the market. R Simon’s dryers had proven compatible with Kemutec’s Cone Mills, and they had worked successfully together on previous projects.
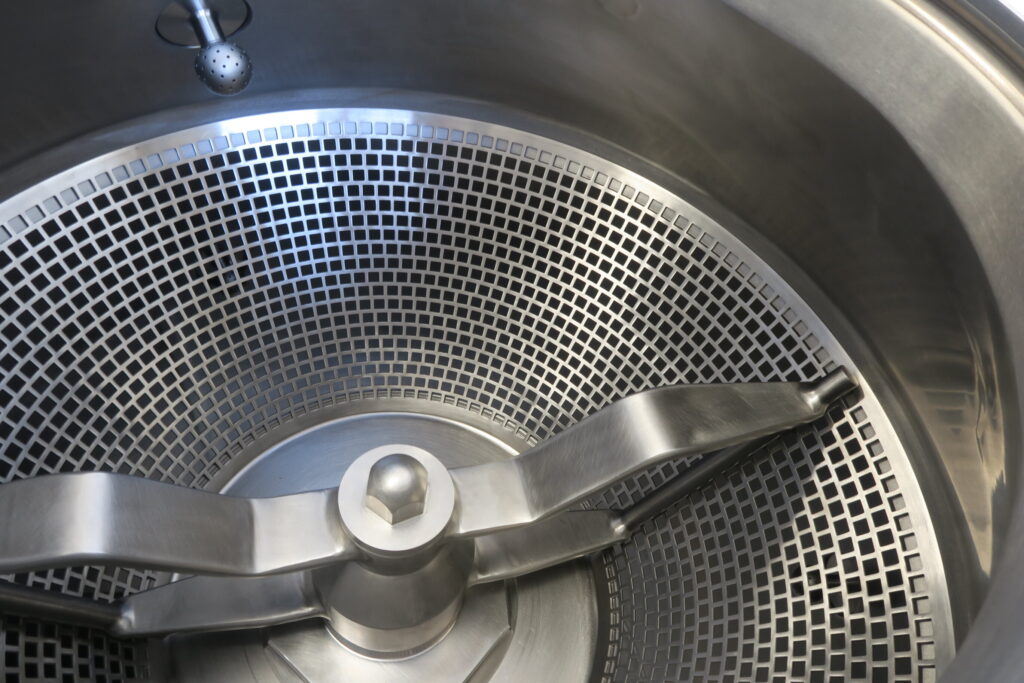
Huntapac formulates strategy to avoid food waste
Huntapac wanted to develop a new product line to make use of the bruised and battered vegetables, which are unable to be sold to supermarkets. The produce still holds its nutritional value but had previously been going to waste, disposed of via a waste disposal company or used to feed livestock.
Huntapac devised a strategy to minimise waste and a process which would convert the damaged vegetables into powder. As part of this process, the vegetables would be pulped, dried and then milled to spice-like fineness. They would then sell the vegetable powder for use in food ingredients, soups, stocks, pet food, etc. Developing this new service line required investment in building a purpose-made facility.
Pilot testing program ensures product feasibility
The Kemutec Test and Innovation Center, located in Manchester, UK, supports customers’ individual needs throughout various sub-industries and applications globally. It provided Huntapac with an opportunity to assess whether their design would meet the fineness and quality of the product that their clients required. Supporting Huntapac with a market-leading, in-house expertise meant the Kemutec team was able to advise during each step of the process, identifying risk and providing invaluable feedback.
Several product trials were held using the KEK Cone Mill before the customer committed to purchasing the machinery. It meant that Huntapac had total confidence in their purchase and could ensure it was fit for purpose before incurring any costs.
Huntapac Produce had customers in place before the build of their facility had even finished; the Kemutec team’s offer to support the delivery of their initial orders reinforced the feasibility of the new product line. Kemutec replicated the processes precisely, manufacturing small production batches; ready to be scaled up when the installation took place. The team provided these sample orders of red cabbage and carrots, amongst other products, to satisfy initial customer requirements on behalf of Huntapac.
The Kemutec CM220 KEK Cone Mill was chosen because of its versatility and ultra-hygienic design, with all contact areas inside the mill easily accessible for cleaning purposes. Each unit can be customized to meet clients’ specific application needs, ensuring the delivery of a solution which is dependable, easy-to-use with optimum reliability every time. The Cone Mill offered Huntapac additional benefits outside of their requirements, such as:
- Precision powder processing requirements
- Versatile grinding performance
- Easy cleaning and maintenance
- Low noise
- Low dust levels
Through application-specific experience and adopting a partnership approach with Huntapac, Kemutec was able to provide a higher level of support than the customer initially anticipated. By providing reliable, cost-effective, highly tested solutions, the team at Kemutec supports customers like Huntapac in exploring potential new, revenue-generating service lines while optimizing food usage.
“Using Kemutec’ s KEK Cone Mill, our business was able to successfully start a new product line that repurposed bruised vegetables that still held all their quality nutrients and re-work them into vegetable powders,” shares Will Hunter, Operations Director at Huntapac. “By partnering with Kemutec, we could test our new sustainable process and ultimately make the highest quality product for our customers. By reducing unnecessary waste, we’re proud to be making even better use of our produce.”
Related articles
Stay connected
Subscribe to keep up to date with current perspectives, events, white papers and more.